The importance of Quality Assurance
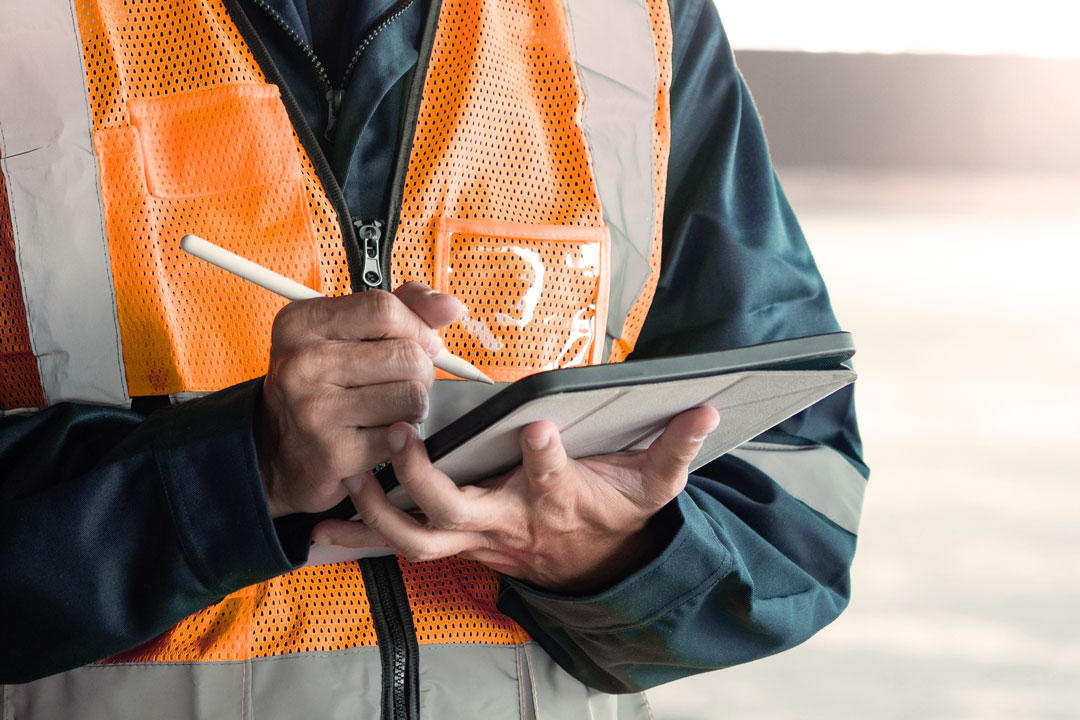
In this Blog Fleetclear Technical Director, Chris Waller explores the vital role of Quality Management in ensuring consistency and product reliability when manufacturing, importing and supplying electronic technology, to avoid expensive issues further down the line.
What is Quality Assurance?
If you are a manufacturer, importer, or supplier of electronic technology, it’s essential to have the necessary controls in place to ensure quality standards are met. Quality Assurance is the framework for ensuring conformity to quality standards and runs at the heart of any reputable business.
Why is it important to us?
Quality Assurance is all about delivering the best products and services for our customers, it ensures all the important processes are followed to reduce the risk and ensure consistency of our products before they reach the market, reducing expensive failures in the field.
We’re proud of our brand and our heritage, from ISS (Innovative Safety Systems LTD) to Fleetclear.
We are a recognised brand within the fleet management and vehicle safety industry and known for means-tested and fit-for-purpose solutions; a reputation we dedicate ourselves to uphold.
We design, manufacture and supply safety solutions for commercial vehicles, including auto-braking reverse radar, anti-roll away, Driver ID and Cyclear™ our bespoke cyclist safety system. Stringent quality measures are essential for systems designed to protect drivers and assist safe operations.
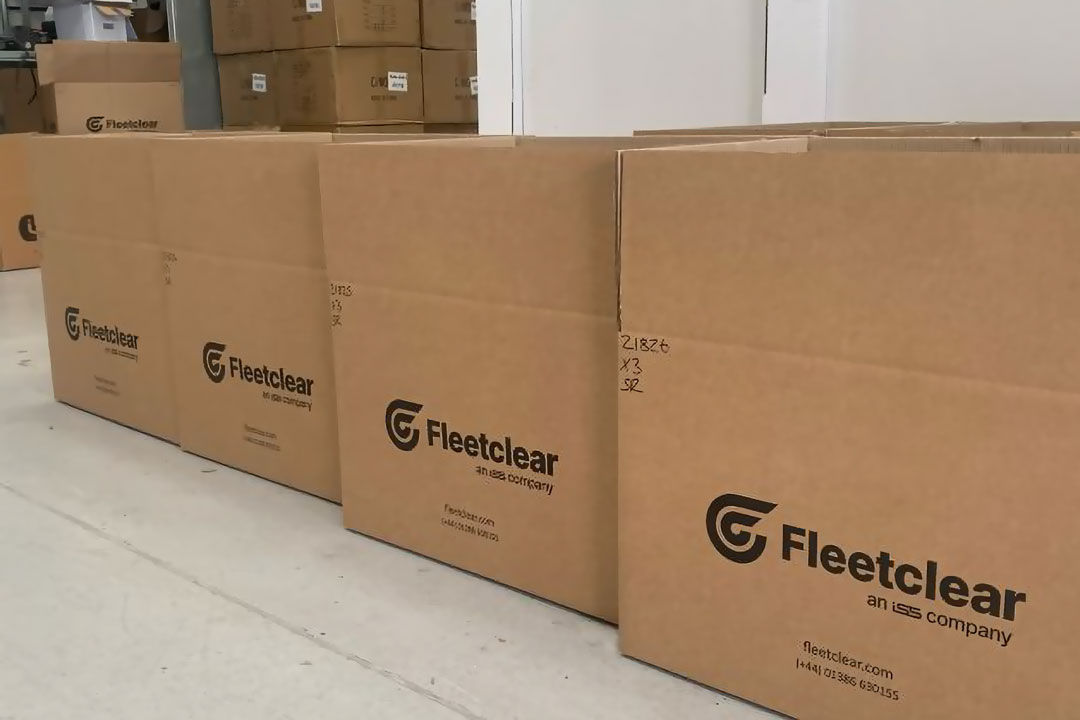
Why is this important to fleet operators?
Markets are flooded with cheap electronic products and reckless suppliers that are attracted to a quick sale. Incredibly, some products even penetrate the professional market and are relied upon by fleet managers in safety critical operations. Poorly regulated electronics can adversely affect other equipment (including that which is safety critical), and lack of control on components and other materials can accelerate degradation, resulting in early replacements, unnecessary out-of-warranty charges, vehicle downtime and sometimes even accidents.
The other major concern for fleet managers is accountability; when your technology fails, who is responsible? Who will put it right? The first and most crucial step to gain Quality Assurance is to validate your supply chain.
How do you find a suitable supplier?
At Fleetclear, we design, manufacture and supply many of our products in house, and we face the same challenges as anyone else when sourcing products, so we operate stringent control procedures to qualify our sources through our supplier assessments. Depending on the type of product, this can include site audits, references, copies of appropriate conformity accreditations, financial audits and cybersecurity/GDPR risk assessments. Thorough supplier assessments are an essential foundation for quality assured products.
How do you know if a product is fit for purpose?
Product testing and certification is the next step, and this includes gaining legislative compliance: regulations such as UNECE Reg 10.05 (the European standard for electromagnetic compatibility in the automotive sector) provide compatibility assurance on individual electronic components and systems.
Certified products will bear an ‘E-Mark’ which is a good indicator of a quality assured component, but the requirement doesn’t end there.
If you are a supplier, you have a duty of care outside of legislation, and you need to understand the intended application to be able to fulfil your obligations. The scope of your product assessment may also need to include safety, technological, environmental, durability, and life expectancy considerations before you approve a product for sale.
Great, now we’ve got a credible supplier and reliable product, job done?
Absolutely not. Customers expect the quality and compliance level to remain consistent throughout your supplier relationship. Poor foresight, lack of control on supply chain and pressure from global electronic component shortages tempts suppliers to use substitute or even ‘grey market’ components, meaning you could be buying a product that looks the same, but underneath it is completely different. If this happens, previously obtained certification would no longer apply either. Signed assurances from manufacturers that products will be delivered to your agreed specification each time are necesary, but they’re not enough. Golden sample inspections, strict change control procedures and regular legislative reviews should all be included in your control plans, and play their part in maintaining consistent supply.
Is all of this really necessary?
Operating without a suitable quality management system exposes you to risks, product failures, bad reviews and unhappy customers, and that’s bad business. We repeatedly see companies prioritise price over quality, but this approach is often more expensive in the long run, and the journey isn’t great either.
Fleetclear’s internal quality department is headed up by Chris Fletcher (pictured left); Chris has over thirty years of experience working in aviation and automotive electronics sectors, and safeguards our quality standards, and leads our drive for continual improvement. “Our robust Quality Management System gives us the confidence to offer industry leading on-site warranty on our products, providing peace of mind and Quality Assurance for fleet managers, so they have one less thing to worry about.”
Quality Assurance made clear: Establish a reliable supply chain, properly capture, and evaluate your product requirements, monitor your supply, maintain control, and continually improve.
Drive your business forward with Fleetclear.
Contact our team to book a demo and start your journey towards a safer, more efficient and compliant fleet.
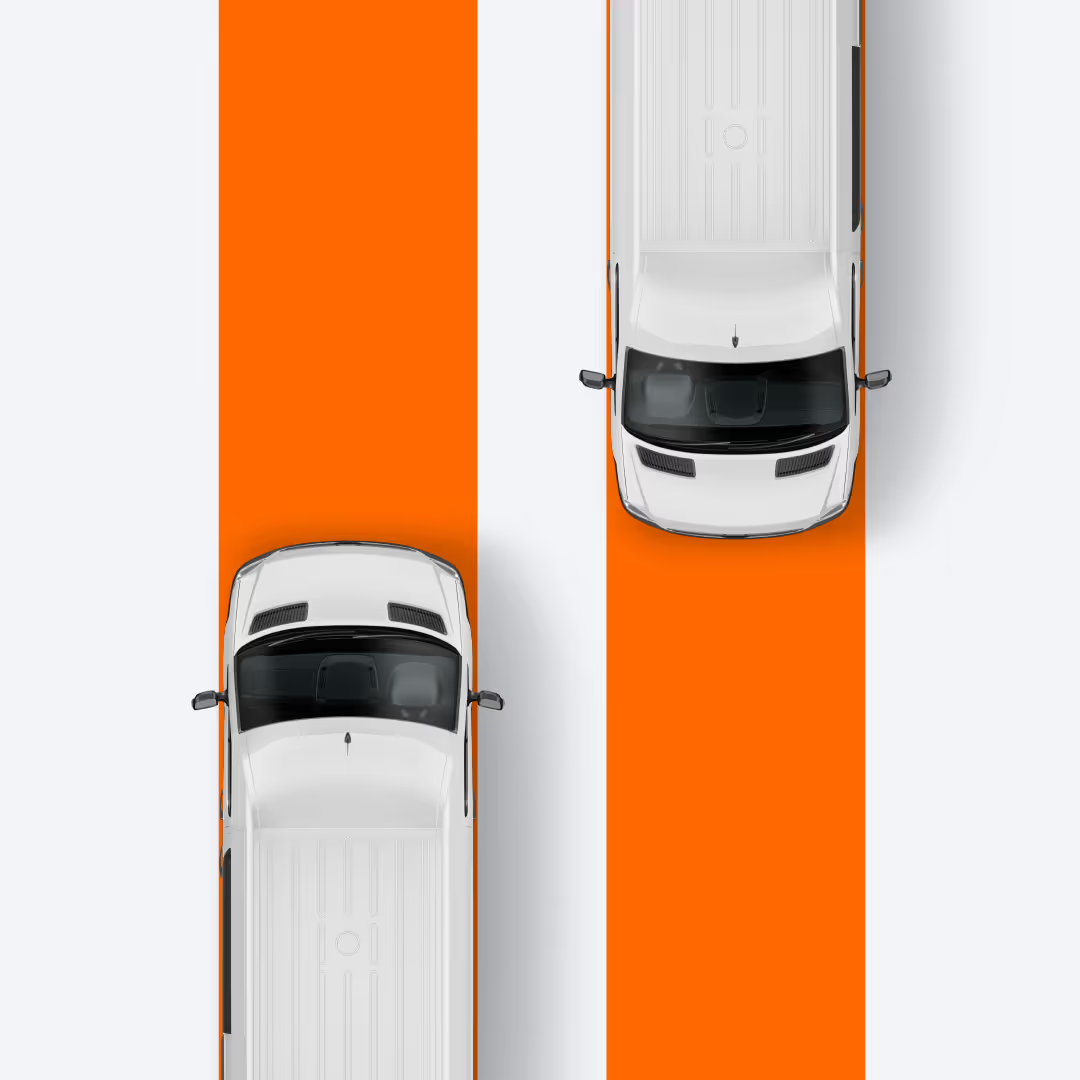